Mastering Precision: A Comprehensive Guide to Advanced Tools in Pouch Cell Fabrication
Posted by Marketing Team on

Pouch Cell Fabrication is a series of processes where each stage contributes to the quality and efficiency of the end product. Starting from slurry making, coating, electrode making, assembly and sealing- this comprehensive guide will tackle each stage on how key factors affect the precision of each process and quality of the pouch cell, and what specific advanced tools can help overcome the challenges easily.
Part 1: Slurry making

The quality of electrode sheets is tied to slurry quality, with around 70%, while pouch cell battery’s overall quality is linked to around 70% of electrode sheets’ quality, hence, making the slurry making as the bedrock for other processes. It contributes around 50% of the whole pouch cell battery make-up which mostly defines the battery performance. Achieving precision in mixing is important as it provides uniformity in electrode thickness and proper dispersion, directly impacting the safety and quality of the battery. Two key factors that are considered in this stage are the uniformity of the material particles and the quality of the electrode sheet. Inhomogeneity poses a significant risk, especially when there are larger particles, leading to multiple stress points and internal short circuits during battery cycling.
The said key parameters are maintained by a vacuum drying oven and vacuum mixer. The application of each piece of equipment results in the best possible slurry, ensuring the required viscosity and solid content for better and high-performing battery electrodes. The vacuum oven is designed for delicate substances, such as the slurry for the pouch cell battery, that is sensitive to heat. The controlled vacuum and inert gas pressure of the drying oven prevent irregularities such as oxidation. The vacuum mixer does the slurry mixing and addresses the inhomogeneity issue by providing gas-bubble-free blending of metals under a vacuumed environment, mixing and breaking the crystal particles, and evenly mixing them.

Battery technology is pushed further by the MSE PRO Lab Vacuum Drying Oven and MSE PRO Compact Dual-Shaft Lab Scale Planetary Vacuum Mixer as they play an important role as these tools provide support and precision in slurry making for pouch cell fabrication. Using these pieces of equipment will provide quality and uniform electrode sheets that mostly determine the Li metal pouch’s safety and overall performance.
Part 2: Coating
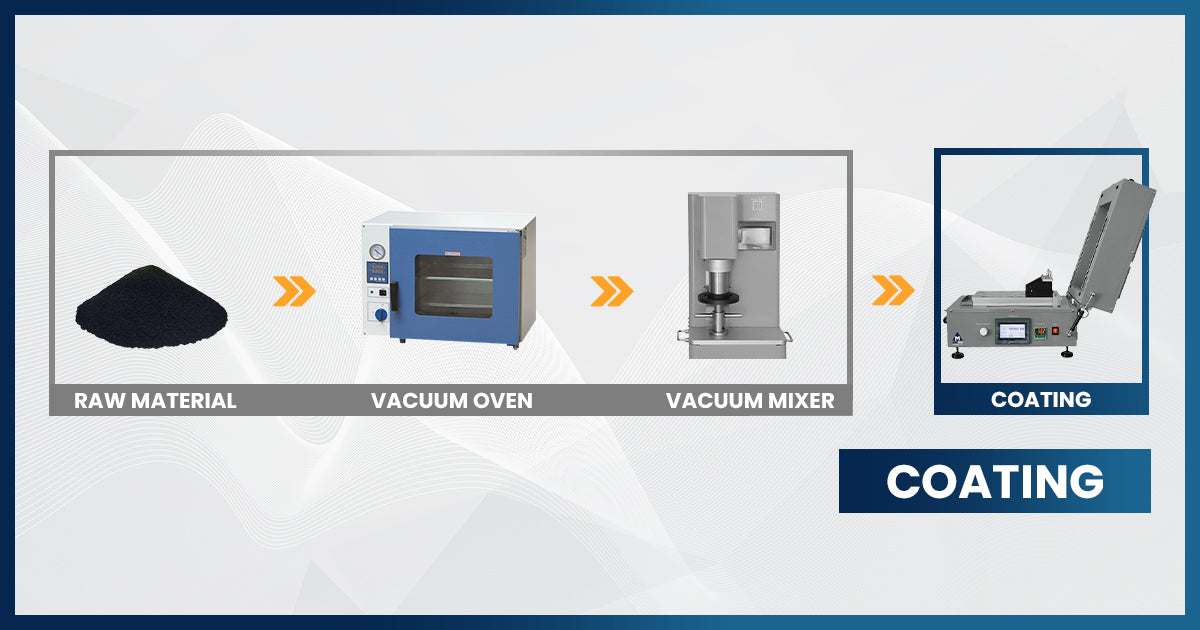
The Coating stage requires tremendous control over electrode thickness as it will ensure consistent electrode thickness, particularly with thicker coatings, and avoid having issues like “heavy edges” from uneven distribution of slurry that counts for optimal battery performance. Maintained uniform coating thickness that meets manufacturer specifications does influence the final cell performance and also prevents issues such as deformation, stress and potential self-discharge or internal short circuits.
Cutting-edge equipment is used to overcome the challenges posed by heavy edges and ensure uniform electrode thickness. MSE PRO Automatic Film Coater features a heating dryer, vacuum chuck and adjustable film applicator that is created to produce films with consistent thickness. The details on this tool such as the flat vacuum chuck and pump enhance substrate adhesion that is beneficial for coating soft and thin substrates, and the micrometer-adjustable film applicator ensures precision that helps cater to specific requirements in a lab-scale coating process.

Having a tool specifically designed for battery electrode coating ensures a better quality product without compromise. The film coater integrated with heating capabilities has a unique driving system to ensure smooth coating on all types of substrates and enables fast slurry drying and coating for temperature-sensitive materials. With the industry’s high standard, cutting-edge tools like this profoundly contribute to overcoming irregularities and achieving consistency in the coating process.
Part 3: Electrode Making

This section contains two processes that makeup Electrode making stage: Calendaring and Electrode die-cutting. These processes greatly impact on the pore structure, electrochemical performance and overall mechanical properties of the battery electrode. The calendaring process is responsible for the performance-optimized pore structure. Having complete control over the compaction process is needed, and the effect of calendaring may differ depending on what we used cathodes or anodes, proving that having a highly calibrated instrument is needed. The die-cutting process affects the alignment of the electrodes, which requires precision in the assembly stage that contributes to the final cell performance.
MSE PRO™ Bench-top Electric Hot Roller Press offers variable speed and heating capabilities up to 120°C and is widely employed for electrode sheet calendaring after coating and drying, effectively increasing density. For those not requiring heating, the Bench-top Electric Cold Roller Press is an alternative solution. MSE Supplies offers a solution depending on what you need with the option of customizing the sizes of the roller's width and material.

After the calendaring process, the product is ready for die-cutting. MSE PRO™ Lab Pneumatic Battery Electrode Die Cutter is designed for die-cutting of positive and negative electrode sheets in punching-type cells with a pneumatic method that provides accuracy, an important factor in maintaining the integrity and alignment of electrodes. The machine has a delicate appearance and small size, which can be placed in a glove box.
The calendaring and Electrode Die-cutting process requires equipment that offers precision and solution to anticipated problems. Achieving a performance-optimized pore structure, maintaining mechanical properties and ensuring electrode alignment contribute to the overall quality of lithium-ion battery electrodes, and laying the foundation for high-performance pouch cells.
Part 4: The Assembly System

The Assembly System consists of the following: Stacking, Welding, and Case-forming processes. Irregularities occur such as uneven stress distribution during stacking, electrode shifting due to static electricity, and the risk of internal short circuits caused by improper positioning of materials. The Z-stacking process is used due to its effective stress distribution still needs a strategic separator and anode replacement. The risk of electrode shift occurring during winding shows the importance of proper alignment. Taking these factors into consideration regarding choosing the right piece of equipment and tools will provide structural integrity and optimal performance in Li metal pouch cells.
MSE PRO™ Benchtop Semi-Automatic Electrode Stacking Machine offers stable and repeatable stacking of cathodes, anodes and separators through a “Z” shape stacking path, addressing the issue of uneven stress distribution. This advanced equipment has high compatibility with electrodes top to 200x200mm, offering a wide range of applications.

After stacking, a controlled welding process can be done by a CE-certified MSE PRO™ 800W Ultrasonic Welding Machine. The equipment is designed specifically for welding electrode sheets (Cu & Al) and has glove box compatibility for a controlled environment. MSE PRO™ Bench-top Pneumatic Aluminum Laminated Film Case Forming Machine compliments the equipment mentioned, a key component for preparing pouch cell cases made of aluminum laminated film. Using this specific equipment minimizes the risk of electrode shift because the tool helps in aligning and proper positioning. Having a strategic and tailored solution for each factor that affects every stage streamlines the process, enhancing the battery’s structural integrity and mitigating internal short circuits and other mentioned risks.
Part 5: The Sealing System

On to the final phase of the pouch cell fabrication process, the Sealing System. This includes top and side sealing, electrolyte injection, primary sealing, and secondary sealing with degassing and resealing in the middle. The success of the whole process relies on precision and accuracy because any deviations can greatly impact the performance and safety of the pouch cell battery. The key parameters that we’ll consider in this stage are pressure, electrolyte measurement, and sealing which account for optimal outcomes.
Innovations in compact heating sealers for aluminum-laminated film case sealing have been developed. These machines feature soft sealing bars, ensuring a secure and precise seal for pouch cell batteries. Advancements in electrolyte injection systems and sealing machines bring controlled electrolyte injection, vacuum standing, and electrolyte degassing with a diffusion function. These tools, designed with meticulous attention to detail, cater to the stringent requirements of pouch cell assembly, delivering consistent and reliable sealing.

MSE PRO™ Compact Pouch Cell Aluminum Laminated Film Case Top and Side Sealer adopts a soft sealing bar that provides a high-quality, compact heating sealing solution that can be placed in a glove box. The separate design of the controlling and working parts makes both top and side sealing precision. The Bench-top Vacuum Electrolyte Injection System is a 3-in-1 design that is suitable for vacuum sealing, electrolyte injection and vacuum standing applications. Multiple functionalities offered by the MSE PRO All-in-One Sealing Machine are sealing, degassing and diffusion functions for professional lithium pouch cell battery laboratory research. The removal of air after injecting the electrolyte under vacuum conditions provides better saturation of the electrode, ensuring the best battery charging-discharging performance. This advanced and multi-functioning MSE PRO™ equipment benefits manufacturers and researchers due to its ability to mitigate and minimize challenges imposed by misalignment, electrolyte management and sealing which results in an efficient and reliable assembly process.

It has become evident that precision is not merely a desirable quality but an absolute necessity. Integration of advanced tools ensures the optimization of each stage, leading to pouch cell batteries of the highest quality, safety, and efficiency. The future of energy storage lies in the proper craftsmanship and advanced technology all in every MSE PRO™ product.
Enhance your pouch cell assembly operations with MSE PRO™ scientific supply and equipment, designed to deliver exceptional performance. Explore our range of advanced tools designed to redefine the standards of quality and efficiency in energy storage. Contact us today.
“Elevate your fabrication process with MSE PRO™ – Where Precision Meets Excellence.”
Share this post
- Tags: Brands - MSE PRO, Industry - Lithium Battery & Renewable Energy, Products - Lithium Battery Materials & Tools